Is Your Container Management Solution Ready for AI Inspections?
Imagine this: You have a container that’s been inactive and unseen by your team for the past three months. The shipment is delayed, repair costs are higher than expected, and your team is scrambling to manage the fallout.
Sounds familiar? Don’t worry — you’re not alone.
Manual container inspections have been the industry standard since containerization began. But in today’s high-speed, high-volume logistics world, manual inspections are a major bottleneck.
The real question isn’t whether you need smarter processes — it’s whether your Container Management Solution can support them.
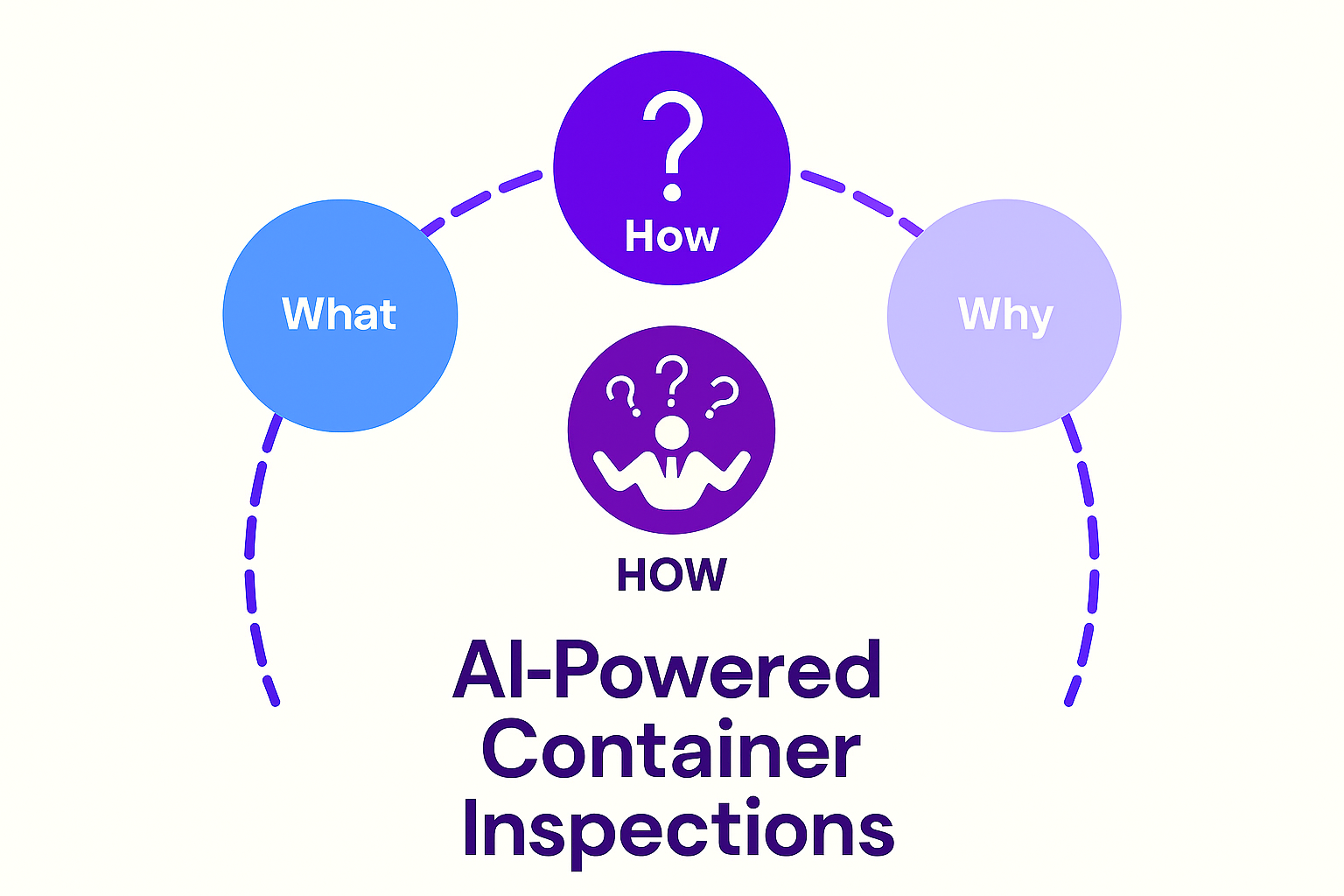
Let’s explore the “why,” “how,” and “what” of AI-powered container inspections — so you stay ahead, not behind.
WHY: Traditional Inspections Are Slowing You Down
Manual inspections are time-consuming, subjective, and unreliable. Even seasoned depot teams face issues such as:
- Overlooked or underestimated container damage
- Disputes over repair estimates
- Long turnaround times
- Lack of audit trail or historical damage records
The result? Higher costs, longer lead times, and declining trust.
Container Management Solutions must evolve — because what worked yesterday won’t work tomorrow. AI offers a faster, more accurate, and more reliable solution.
HOW: AI Enhances Your Container Management System
We’ve introduced an intelligent AI-powered damage detection process into our Depot Management System (DMS) — a vital upgrade to modern Container Management Solutions.
Here’s how it works:
- Inspectors use a mobile app to capture images of each container
- AI models instantly scan the images and flag any damages
- The DMS generates repair estimates using data-driven insights
- Every inspection is logged with a full digital history
- Historical comparisons help reduce repeat issues
WHAT: The Future of Container Management Solutions is AI-Driven
With AI-enabled container inspection now built into your Container Management Solution, you can enjoy:
- Real-time, automated damage detection
- Consistent, audit-ready inspection reports
- Accurate repair cost estimations
- Historical tracking to identify recurring problems
- Reduced dependency on manual judgment
This isn’t just a feature — it’s a competitive advantage. AI-led digital transformation saves time, cuts costs, and boosts confidence from yard to customer.
Ready to Reinvent Your Container Management Solution?
If you’re still relying on traditional inspection methods, it’s time for a change.
Let AI-powered Container Management Solutions help you inspect faster, more intelligently, and with greater reliability — without delays or assumptions.
Get in touch with us and see the future of depot inspection in action!
FAQs
What is AI-powered container inspection?
- AI-powered container inspection uses advanced image recognition technology to detect surface damages such as dents, rust, scratches, and corrosion automatically, improving inspection accuracy and speed.
What types of damages can the AI detect in containers?
- The AI system is trained to identify various surface-level issues, including corrosion, dents, scratches, cracks, and other visible structural irregularities.
Will this AI feature work on all devices?
- Yes, the inspection app is mobile-friendly and syncs image data to the system whenever connectivity is available.
How secure is the inspection data in this system?
- All information is fully traceable, encrypted, and securely stored to meet regulatory requirements and ensure operational visibility.